It’s a small world: 1/6 scale to be exact
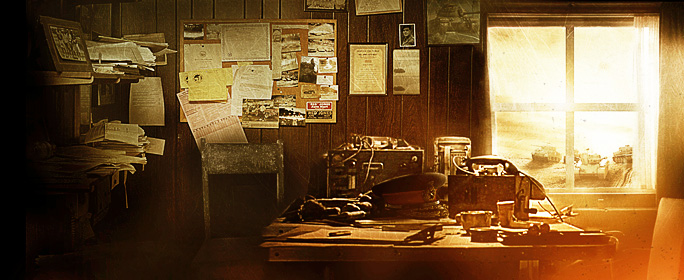
Armortek
I was recently fortunate enough to get invited to the factory of Armortek, tucked away in a beautiful part of the Devon countryside.
Who are they?
Well, any serious modeller would have heard of them, they are, in my opinion, the Rolls Royce of the modelling world. Their reputation for quality, reliability and attention to detail is second to none.
Exclusivity is their middle name: limited numbers (around 30 to 50) of each model are produced, each with a unique serial number. Quality not quantity - this is proven by the sheer fact that 70% of their customers become repeat customers and they ship worldwide.
Remarkably, it’s a two man show, well, two people - Mark and his wife Gill. Mark is the genius behind the research, development and ultimate build. He uses the latest in full three-dimension modelling and software using mainly aluminium alloys in the manufacture. But the mechanical parts (shafts, axles etc.) are machined from steel. Sheet metal parts are all laser cut from steel or aluminium.
![]() This (left) becomes this (right). |
The design process is fascinating from the initial ideas, which usually come from customers, to the research which is all conducted using actual vehicles. Mark refuses to use existing documented measurements or research as he simply does not believe it all to be 100% accurate - many details are often contradictory. A prime example of this is their Tiger 1 model (the company’s best-seller) which was built based on the Tiger 1 at Bovington Tank Museum (UK) for the early and mid-production models. In the case of the later model, they built it based on the Tiger 1 in the Musee des Blindes in Saumur, France.
(Below) Mark –The creative genius.
As a rule of thumb, Mark works on a time frame of 6 weeks for design and prototype and then 4 months for manufacture. This means that the total number of vehicles produced in a year is roughly two and a bit!
(Below) Now that’s attention to detail.
The manufacturing machinery they use is all state-of-the-art, including multi-axis turning machines and machining centres that are all computer controlled.
![]() |
The MKIV (above), complete with 5000 rivets, was commissioned for the Bovington Tank Museum’s new “Warhorse to Horsepower” exhibition.
On the day of my visit, the final museum model was painted by World of Tanks player Paul (Pictured below), completed and made ready for delivery.
![]() |
Every model is available with an “option pack” which truly brings it to life. The motion pack uses industrial control gear and motors to enable the model to move through incredibly rough terrain. The average weight of the tanks is around 170kg and they are powerful enough to pull a 7.5 ton truck.
If you also opt for the special effects packs you also get digitally recorded proportional sound which is about as accurate to the real thing as you will ever get. Add to this the recoil unit and you also get gun sounds and flash.
Foolishly, I was expecting to see a collection comprising every model completed at the factory. The reality was “no” because they all sell well and sell quickly - another indication of both the quality and collectability of these models. In fact, the only model currently in stock is the 25 pounder Field Gun. (Below)
Overall it was a great day with two of the nicest people I have ever met. Their passion for the business and commitment to accuracy is what makes Armortek the best at what they do.
So what’s next on the production run?
In all seriousness, Mark has no idea. “It all depends on what the customer wants” – he said.
So to finish with a question for all World of Tanks players - what would you like to see them build?
Комментариев нет:
Отправить комментарий